Making a new dashboard
15 posts
• Page 1 of 1
I'm contemplating making a new dash for my car using the old 130/5 dash as a template
Looking at the dash, it looks like 7 ply with a walnut veneer and plain veneer (mahogany?) on the reverse. The overall thickness is 10.08mm
I recon that 9mm marine ply would be ok. Has anyone tried this before? Apologies if it's already been covered, I've searchd but not found anything.
Mike
Looking at the dash, it looks like 7 ply with a walnut veneer and plain veneer (mahogany?) on the reverse. The overall thickness is 10.08mm
I recon that 9mm marine ply would be ok. Has anyone tried this before? Apologies if it's already been covered, I've searchd but not found anything.
Mike
- mikealdren
- Coveted Fifth Gear
- Posts: 1194
- Joined: 26 Aug 2006
Sounds good. I haven't made a new dashboard but recently stripped mine down to the ply on the pretty side and refurbished everything. I think the particulars of the plywood aren't super-critical as long as you use something sturdy that won't warp over time. Applying the veneer was super-easy; I'd never done that before but had no trouble with it.
Go for it; you'll probably do well and you'll end with something to be truly proud of.
Go for it; you'll probably do well and you'll end with something to be truly proud of.
1970 Elan Plus 2 (not S) 50/2036
2012 BMW R1200GS
"It just wouldn't be a complete day if I didn't forget something!" -Me
2012 BMW R1200GS
"It just wouldn't be a complete day if I didn't forget something!" -Me
-
The Veg - Coveted Fifth Gear
- Posts: 2185
- Joined: 16 Nov 2015
Thanks veg, my main concern is getting the thickness right though I'm not sure how critical it is.
- mikealdren
- Coveted Fifth Gear
- Posts: 1194
- Joined: 26 Aug 2006
Made a custom Dash for one of my Classic Mini's and was advised to use Marine Ply so looks to me like you are on the right track
Good luck with the project, would be nice to see some pictures of the progress so others might follow where you lead
Good luck with the project, would be nice to see some pictures of the progress so others might follow where you lead

Simplify and add lightness
Lotus Elan S4 Coupe - Wedgewood Blue
Lotus Elise S1 - Racing Green
Lotus Elan S4 Coupe - Wedgewood Blue
Lotus Elise S1 - Racing Green
-
Rob P - Second Gear
- Posts: 177
- Joined: 10 Jun 2014
My S2's had a marine plywood dash for probably over 30 years now and it's held up well. It was originally just stained a blonde color. In my current disassembly, I removed the dash and sanded and re-stained it (then had someone else do it since I did a lousy job!) - color-wise, it's now darker and closer to the original color but at the point where if it's sanded any more, it'll need replacing (or veneering or something - I know very little about wood finishing.)
This is what it looked like after sanding, before staining. Note that it's sitting on a Ron Hickman-designed B&D Workmate.
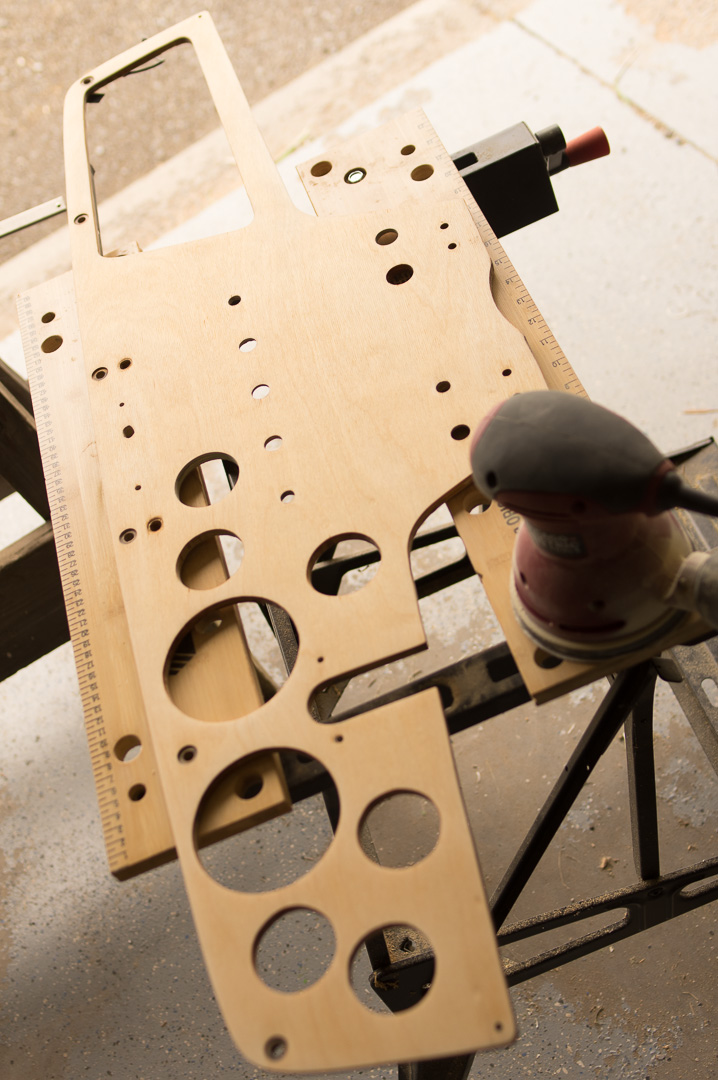
This is what it looked like after sanding, before staining. Note that it's sitting on a Ron Hickman-designed B&D Workmate.

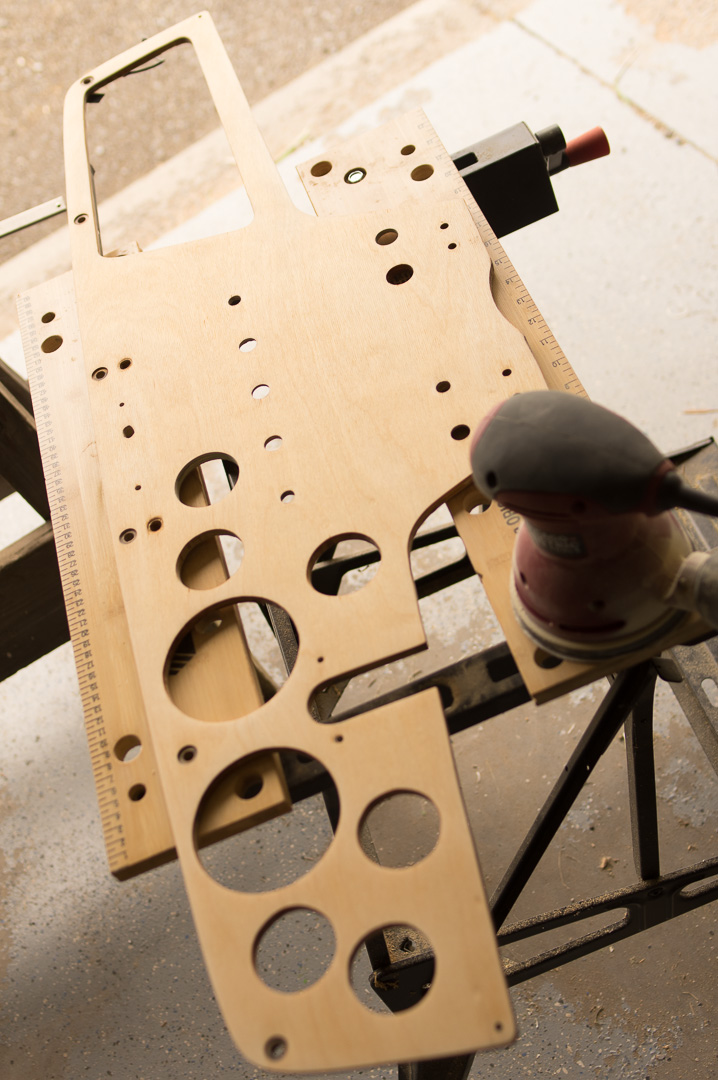
Jeff Kyle
1965 Elan S2
2005 Elise
1965 Elan S2
2005 Elise
- groucho
- Second Gear
- Posts: 87
- Joined: 12 Nov 2009
I'm about to do a whole new one for my +2. I want to re-arrange a few things as I'll be finding a home for the aircon controls and maybe another vent.
Should the veneer go on before or after cutting the holes for gauges etc?
Should the veneer go on before or after cutting the holes for gauges etc?
Chris
Elan +2 #0245
Exige S2 Supercharged
Elan +2 #0245
Exige S2 Supercharged
- Chrispy
- Third Gear
- Posts: 309
- Joined: 29 Oct 2017
A thread on your AC install would be appreciated, as will likely do it on my car at some point so interesting to see how you approach it and parts used etc.
I believe you add the veneer after cutting the holes in the plywood and a suitable sharp knife can be used to cut the veneer.
I believe you add the veneer after cutting the holes in the plywood and a suitable sharp knife can be used to cut the veneer.
'73 +2 130/5 RHD, now on the road and very slowly rolling though a "restoration"
- mbell
- Coveted Fifth Gear
- Posts: 2643
- Joined: 07 Jun 2013
I have reveneered three of them. Two were easy, one was hard but more satisfying. My Europa and series one Elan were done using wood veneer that comes with a paper backing. Walnut for the Europa and teak for the Elan. The advantage to this is that the material is very smooth and flat, very easy to work with. Just cut out a piece large enough to do the job and glue in on. I used another piece of plywood and weighted it in place to keep it flat while the glue cured. The disadvantage is that the actual wood is very thin so sanding must be kept to a minimum, but it is very smooth to start with and requires very little finishing. The walnut was finished with automotive clear coat, the teak with just an oil finish.
On my +2S I used real walnut burls. I could not find it paper backed. It comes in filches, a pack of veneer with as many sheets as your purchase. The burls are small and have to be bookmark pieced together, mine took four pieces with a seam down the center vertically and a seam horizontally about mid ash tray. The wood is very dry and wrinkled and I was not sure how to hold it flat. I decided on a vacuum bag. I learned how to do this by searching the internet and u tube videos. I have posted some pictures. I used lectraset press on transfer individual letters to label the dash, I purchased them from an artist supply house for the Europa 30 years ago and had enough left to do the +2S. Don't know if they are still available and I was amazed that I still had them after all these year. I used West system epoxy to laminate all of the veneers and it has held up perfectly, The automotive clearcoat has suffered no cracking and no veneer lifting. I probably could have purchased a new dash from a supplier for about the same cost as the supplies but had a good time and learned a new skill. The photo of the dash in the vacuum bag has the veneer down on a flat surface with the back of the dash covered with a dispersion layer to allow the air to exit, then the bag with the vacuum drawn down. The epoxy took a couple of hours to cure with the vacuum held the entire time. With the valve closed it would hold with the pump off, but I did have to pump it down a couple of times in the cure cycle. No stain on the wood, just clear coat. Cut the holes for the guages and switches with a sharp exacto knife after cure. Same with the glove box door and radio blanking plate, then letter and clear. Gary
On my +2S I used real walnut burls. I could not find it paper backed. It comes in filches, a pack of veneer with as many sheets as your purchase. The burls are small and have to be bookmark pieced together, mine took four pieces with a seam down the center vertically and a seam horizontally about mid ash tray. The wood is very dry and wrinkled and I was not sure how to hold it flat. I decided on a vacuum bag. I learned how to do this by searching the internet and u tube videos. I have posted some pictures. I used lectraset press on transfer individual letters to label the dash, I purchased them from an artist supply house for the Europa 30 years ago and had enough left to do the +2S. Don't know if they are still available and I was amazed that I still had them after all these year. I used West system epoxy to laminate all of the veneers and it has held up perfectly, The automotive clearcoat has suffered no cracking and no veneer lifting. I probably could have purchased a new dash from a supplier for about the same cost as the supplies but had a good time and learned a new skill. The photo of the dash in the vacuum bag has the veneer down on a flat surface with the back of the dash covered with a dispersion layer to allow the air to exit, then the bag with the vacuum drawn down. The epoxy took a couple of hours to cure with the vacuum held the entire time. With the valve closed it would hold with the pump off, but I did have to pump it down a couple of times in the cure cycle. No stain on the wood, just clear coat. Cut the holes for the guages and switches with a sharp exacto knife after cure. Same with the glove box door and radio blanking plate, then letter and clear. Gary
- GLB
- Second Gear
- Posts: 191
- Joined: 31 Jan 2018
Mike, I will say that adding extra thickness to the fascia may complicate installation of the steering column covers (between fascia and steering wheel). I've refinished the fascia on my Plus 2S and that fit is tight. Not sure the extra thickness would be a problem anywhere else (though it will push the console back a little, and with it will go the aperture and boot for the shifter.
Just a couple things to consider . . .
Wondering why you don't reveneer the existing/original fascia, seeing as how you'll have to be doing veneer work in any case?
Regards,
Randy
ps. hoping to have more fascia labels printed and on offer in the next month or two . . .
Just a couple things to consider . . .
Wondering why you don't reveneer the existing/original fascia, seeing as how you'll have to be doing veneer work in any case?
Regards,
Randy
ps. hoping to have more fascia labels printed and on offer in the next month or two . . .
-
Sea Ranch - Coveted Fifth Gear
- Posts: 1098
- Joined: 07 Mar 2011
A bit of history...
I have two +2s, both in bits. My aim, now I'm retired, is to build one as a Zetec (in progress) and then rebuild the other.
One car has an original dash, the other a replacement. I have stripped the original dash but carelessly slightly rubbed through the veneer at the edge of the glovebox, very minor but upset my OCD. I did have to repair some lifting veneer, I used waterproof Evostick wood glue, easy to use and you can wipe of any excess with a damp cloth. Gorilla or Epoxy are not so easy. After light rubbing down and varnishing, you really can't see the repair
I used Rustin's 2 pack and the results are good. I will use this dash for the 2nd car.
For the Zetec, I am making some minor adjustments to the layout - no choke etc. Cutting a new piece of ply will be easier than veneering, I'll use the original as a template, cut roughly with a jigsaw and then copy with a router finishing the square corners by hand. The only real questions are whether to use marine ply or birch and what thickness given the exact equivalent doesn't seem to be available. I'm going to my local timber specialist this morning.
I have two +2s, both in bits. My aim, now I'm retired, is to build one as a Zetec (in progress) and then rebuild the other.
One car has an original dash, the other a replacement. I have stripped the original dash but carelessly slightly rubbed through the veneer at the edge of the glovebox, very minor but upset my OCD. I did have to repair some lifting veneer, I used waterproof Evostick wood glue, easy to use and you can wipe of any excess with a damp cloth. Gorilla or Epoxy are not so easy. After light rubbing down and varnishing, you really can't see the repair
I used Rustin's 2 pack and the results are good. I will use this dash for the 2nd car.
For the Zetec, I am making some minor adjustments to the layout - no choke etc. Cutting a new piece of ply will be easier than veneering, I'll use the original as a template, cut roughly with a jigsaw and then copy with a router finishing the square corners by hand. The only real questions are whether to use marine ply or birch and what thickness given the exact equivalent doesn't seem to be available. I'm going to my local timber specialist this morning.
- mikealdren
- Coveted Fifth Gear
- Posts: 1194
- Joined: 26 Aug 2006
Donels wrote:Veg, I have contemplated re-veneering my dash but have been put off by what I?ve read. Could you tell me how you did yours please.
Dave,
To expand a bit on what GLB said, it's fairly simple and the fibre- or paper-backed veneers are the easiest to work with since they are already pressed smooth. I found some at a local specialty-woods shop, a real treat of a place that's like walking into a humidor. If no such shop is near you, you may be able to order online. I got a nice piece of burl walnut but unlike most, I went with a piece that is NOT bookmatched, as I thought it had more character.
My old veneer was really easy to remove as it it was wrinkling and loosening since the adhesive had degraded into something resembling powdered chalk. A putty-knife dispatched the more resistant bits, then a light sanding cleaned up the plywood.
To apply the veneer, first I eyeballed it to see which orientation and general positioning on the dash would maximise the visual characteristics of the veneer, and traced the dashboard outline on the back of the veneer to align to.
Then I prepared for the job. I did the gluing in a room that had low-pile carpet over a concrete slab floor, and I borrowed a glass table-top from elsewhere in the house and placed that on the carpet for a hard, smooth, flat surface. Then I covered the glass with some plastic sheet, probably not necessary but it couldn't hurt. Then I laid the veneer on the plastic with the pretty side down. The next step was the glue. I used Titebond III on the advice of the shopkeep at the wood place; I don't know if it is available over in your part of the world or what is equivalent if not, but you want a good sturdy wood-glue that won't be much affected by moisture over the long term. I used an old plastic card (any credit card or hotel key-card will do) to spread the glue thinly and evenly, taking care to keep it thin near the edges, especially the edges of holes, so it wouldn't squeeze-out and form a hard blob that could foul the knife during trimming.
Then I placed the glued board face-down onto the veneer, lined up with the edge tracing, and placed a lot of heavy things onto it such as dumbbells and stacks of books. I gave it a couple of days to fully cure.
Trimming was simple- I used an X-Acto-type knife with a #11 blade and went slowly, taking time to let the knife do the work. The veneer is thin enough that one of these hobby knives is all you need to cut out the holes and trim the edges. Just keep the blade as close as you can to perpendicular with the surface and follow the edges. You don't have to be super-close on the first pass, and in fact it is easier to remove rough chunks first then do the fine carving along the edges. I did save the removed bits to use as test-pieces for finishing and labeling.
Minimal sanding is needed with these pre-pressed, backed veneers, but I used some very fine paper to take it from basic smooth to baby-butt smooth.
I did find a spot where a tiny piece of veneer came loose from the backing. The piece was gone, so I made a filler by taking some of the veneer scraps and sanding them to super-fine dust and then mixing that dust with some of the polyurethane finish to form a paste, then using a plastic card to spackle the hole. Once that hardened, light sanding made it perfectly level with the surrounding surface but using the plastic card's edge over it while applying kept that need to a minimum.
I used spray-can polyurethane to finish, and before applying the last couple of coats I applied new labels, which were dry transfers that I had specially made. There's information about that elsewhere in the forum and in the parts for sale section you can find a thread by a guy who used the same supplier and improved on the set I had made, adding some additional details. The supplier who made the transfers should still have the pattern to make more.
One thing to take care about with the finish is to make sure that globs of it don't run over the edges into the holes, as you don't want to make the holes smaller. I made sure that the edges got a basic coat but no more, as the instruments fit rather closely. There's more room around the switches and I did want what would be visible of the edges of their holes to look good so I applied a little more there.
With the finish dry and hardened, I buffed it with a cheep random-orbit polisher and some very fine auto body polishing compound. I didn't go for mirrory perfection as that would be out of place against all the car's other patina, but I got it to the point of looking good.
1970 Elan Plus 2 (not S) 50/2036
2012 BMW R1200GS
"It just wouldn't be a complete day if I didn't forget something!" -Me
2012 BMW R1200GS
"It just wouldn't be a complete day if I didn't forget something!" -Me
-
The Veg - Coveted Fifth Gear
- Posts: 2185
- Joined: 16 Nov 2015
15 posts
• Page 1 of 1
Total Online:
Users browsing this forum: No registered users and 14 guests